The RECICOM project has enabled the recovery of carbon fiber from end-of-life composites and its integration into new 3R materials for aeronautical applications, such as drone manufacturing.
CIDETEC Surface Engineering has actively participated in the recently completed RECICOM project, which aimed to advance greater sustainability in the aeronautical sector through the development of innovative solutions for the recovery and reuse of composite materials. Coordinated by TITANIA, the project also involved the collaboration of FLUIDMECANICA SUR, DRONETOOLS, I-PUNTO END, and the University of Cádiz.
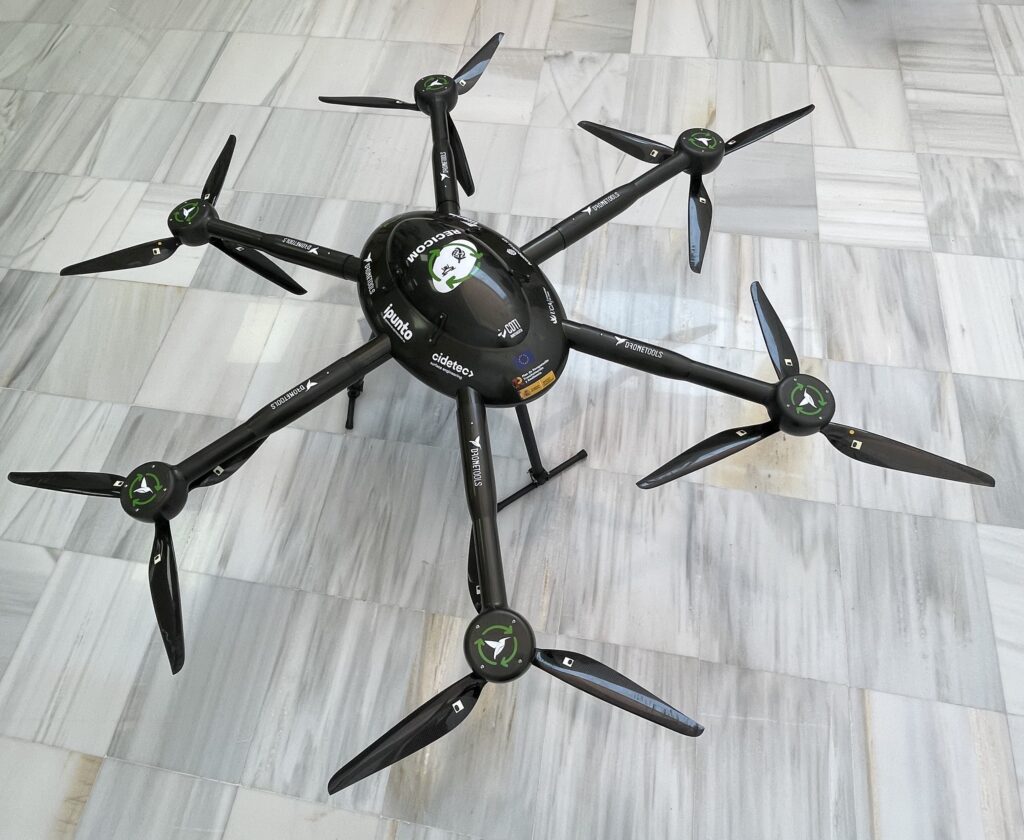
CIDETEC Surface Engineering developed its own formulation of 3R composite (repairable, reusable, and recyclable), which was used to produce prepregs reinforced with carbon fiber to manufacture a drone demonstrator, so that at the end of its useful life, the carbon fiber can be recovered for new use. This innovation has been key in building a final demonstrator: a large drone entirely made with this new 3R material patented by CIDETEC Surface Engineering.
The RECICOM project has comprehensively addressed the challenges associated with both repairability during the life of aeronautical components and their recyclability at the end of it. This represents an important step toward the design of lighter, more sustainable structures that are adaptable to the circular economy requirements of the sector.
In this way, CIDETEC reaffirms its commitment to innovation in advanced materials and their practical application in technological solutions that contribute to a more sustainable future.